      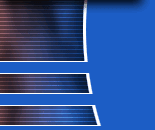
    
        
|
|
|

Solid, semi-tubular and tubular rivets are
widely used mechanical fasteners. These specific types of rivets are
employed in a wide variety of products which may require flexible
joints or tightly joined mating components. Typical solid rivets
include flat head, pan head, round head and shoulder type rivets. The
head may be of various shapes and the shank must be of sufficient
length to accommodate the thickness of the parts to be joined and to
allow for the formation of the clinch head. Solid rivets are available
in many metals and alloys to meet today's requirements of tensile and
shear strength, electrical conductivity, corrosion resistance,
appearance and cost. Flat head, pan head and button head rivets are
more commonly used for tightly joining mating components.
Shoulder-type rivets are normally used for pivoting or hinging joints.
A basic requirement of the rivet is that the material must be able to
withstand rigorous cold-working without deterioration and provide the
desired standards of finish and appearance. Two of the most common
types of steels used in rivet manufacturing are SAE 1010 from which
cold-headed rivets are made and B1113, or screw machine steel. Brass,
nickel-silver, bronze, copper, stainless steel and aluminum alloys are
also widely used. In the case of rivets made from SAE 1010, the clinch
head can be easily formed and will provide excellent appearance.
Rivets of B1113 steel do not lend themselves nearly as well to the
riveting process and on this type of rivet the formed closure is
usually ragged around the edge and has a poor appearance. There
are four principal ways to clinch solid, semi-tubular rivets or
studs-staking, spin roller forming, orbital forming, and radial
forming. Each of these have variations in tooling and technique. Each
has advantages and disadvantages.
Staking
operations cover a wide range of techniques and applications. Staking
in general is a fast low-cost method of heading solid, semi-tubular
rivets or studs where a head with a smooth finish is not required. The
operation is most likely performed in a press or a rivet setting
machine, and clinch formed with a tool having a shaped face. The tool
does not revolve. Tool pressure alone reshaped or cuts back the rivet
shank, rather than flowing the metal. Speed and low costs are the
principal advantages of staking. The performance cycle is rapid, and
tools and equipment are of the simplest kinds. A
disadvantage is the lack of holding strength in the staked end. Hence,
the method is not recommended for parts which must resist pulling
apart in the direction of the rivet and resist high torque on the
head. The appearance of a staked rivet is not compatible with high
quality work.
Twin Spin Roller
Forming of clinch head: -achieved with Twin-Spin tooling is
designed to utilize the combined forces of motion and pressure. The
Twin-Spin tool consists of two matching, precision shaped, hardened
and polished steel rollers. These are contained in a tool holder just
slightly larger than the diameter of the work piece. The rollers
distribute a combination of forces which flow the material to the
desired shape and size. The material is flowed from the center
outward, in a radial series of overlapping waves. Since the material
is flowed continuously in these two directions, spin roller forming
produces the highest quality grain structure, head integrity, and
uniformity of head structure. In a typical Twin-Spin application
such as head-forming on rivets, pins, or staking posts, the tool is
brought down on the area to be formed. The free-spinning rollers,
driven by contact with the work piece, rotate counter to each other.
The two rollers always work diametrically opposed, thus counter
balancing each other and applying negligible torque or bending
movement to the work piece. Tightness of the fastener - either loose
to provide free movement of the assembled parts, or tight to prevent
movement - is controlled by roller shape and the amount of pressure
applied. Because of the high degree of control achievable with this
method of forming, there is no deformation of the pin or the fastener
shank. The tightness of the rivet in the joint can be controlled
within close limits and with excellent repeatability. Surface
finish is polished in appearance, and head integrity is excellent. The
maximum shank diameter of the work piece is limited only by the output
of the power head. Depending on size or material, forming cycle time
ranges between one quarter to one second. Possible
disadvantages of this method for certain classes of work may be the
relatively large diameters of the roller tools, which prevent riveting
in extremely close quarters, or the need to use a lubricant with some
materials. Carbide tooling is supplied when lubricants can not be
used. All Grant Riveter's automatically supply a very thin film of
lubrication to the hidden side of the twin spin roll forming die's.
Lubrication greatly increases life beyond belief. One set of rollers
made from Grant's coated high grade tool steel or made from carbide
have been tested in high-end production environments where the dies
produced production for over a year.
Orbital Forming
is also commonly used in producing heads on rivets, pins, or posts.
Orbital tools are composed of a rotating tool holder and a shaped tool
insert. The axis of the tool insert has a definite angular
relationship to the axis of the tool holder. The forming end of the
insert is located at the intersection of these two axes. The insert
does not rotate when in contact with the work piece, and as a result,
describes a concentric, conical path…. very much like a top beginning
to run out. The rivet or pin being worked, is "set" by a
combination of pressure, high speed spinning action of the holder, and
conical rotary motion. The operation is quiet and produces
joints and heads of high quality, at high cycle speeds. Design of
tools can be adapted to work in close quarter. Orbital tools can be
adjusted to produce a tight or loose assembly, and lubricants may be
required for a better finish. Orbital tooling is generally set up to
produce extremely tight assemblies where no movement is acceptable.
The disadvantage of the orbital forming process is that the initial
tool holder is relatively expensive. However, tool inserts - although
more expensive than Twin-Spin rolls- have excellent life. The grain
structure of orbital formed heads is not of the quality obtained with
Twin-Spin rolls and radial forming. The rivet or pin being worked in
an orbital form technique, can not be headed without deformation of
the shank under the formed head. The cosmetic's are generally very
good.
Radial Forming
is another popular process used in producing heads on rivets, pins or
post. Different than the circular motion of the orbital tool, radial
riveting passes the tool through a rosette forming pattern. Each
rosette path or loop pass through the center, the longitudinal axis of
the riveting tool always overlaps the center of the rivet. The
material is spread radial from the center outward and looping inward
rather than around the center. According to the practitioner the rivet
material is spread in a radial manner or formed tangentially
overlapping. The operation is quiet and produces joints and heads of
high quality and slightly polished in appearance. The tools can be
adapted to work in close quarter. Radial forming can be adjusted to
produce a tight or loose fastener. The grain structure of a radial
formed head is not as high in quality as spin roller formed heads. The
control of a joint can be held within limits slightly better than
orbital forming but falls short of Grant's Twin Spin roller forming
process. The Grant process is much quicker with better results.
Complexity of radial motion generation is
considered by some as a process disadvantage. Other problems
encountered are: poor power train wear factors under heavy forming
condition; forming tools cost more to manufacture than orbital tool
inserts; The rivet or pin being worked, can not be headed without some
deformation to the fastener shank; cosmetic appearance is only fair to
good; length of forming pass increases cycle time considerably.
In conclusion,
all four principal ways to clinch form solid, semi-tubular rivets or
studs by staking, spin roller forming, orbital forming and /or radial
forming, all have advantages and disadvantages. Each process has
unique in its capabilities. There is no one best process that meets
the needs of all heading operations.
The "Grant" Solution
provides the most cost effective way to form or fasten a rivet or
component without hindering the performance or the integrity of the
rivet or part being fastened. "Grant" employs several processes all
adaptable within a single modular unit portable power head riveter.
Any "Grant" power head can accept orbital, twin-spin roller forming,
multi-spin roller forming, spin-press (burnishing), chamfering tools,
drilling and even rolling or cutting threads. Riveting has grown
into an age of modularity and portable riveters.
There are two basic
power head designs that assure a future for riveting
assembly. The first is a power head in which the pneumatically,
hydraulically or servo-electric advanced piston encloses a precision
spindle and bearing shaft assembly. This one design feature allows us
to manufacture a durable head, simple to maintain, low in initial cost
and economical in operation. The second is a power head in
which the pneumatically or hydraulically operated piston has a complex
eccentric shaft arrangement built within the piston. This spindle
assembly drives a gear arrangement, which controls the radial rosette
forming pattern. The forming tool must complete 360 degrees around the
rivet shank. Because of its complexity maintenance of this type
head, along with its high initial cost, remain operational concerns
which must be over come. One of the units advantages is that due to
minimal side loads it can be operated with simple low cost support
fixtures.
|
|
 |